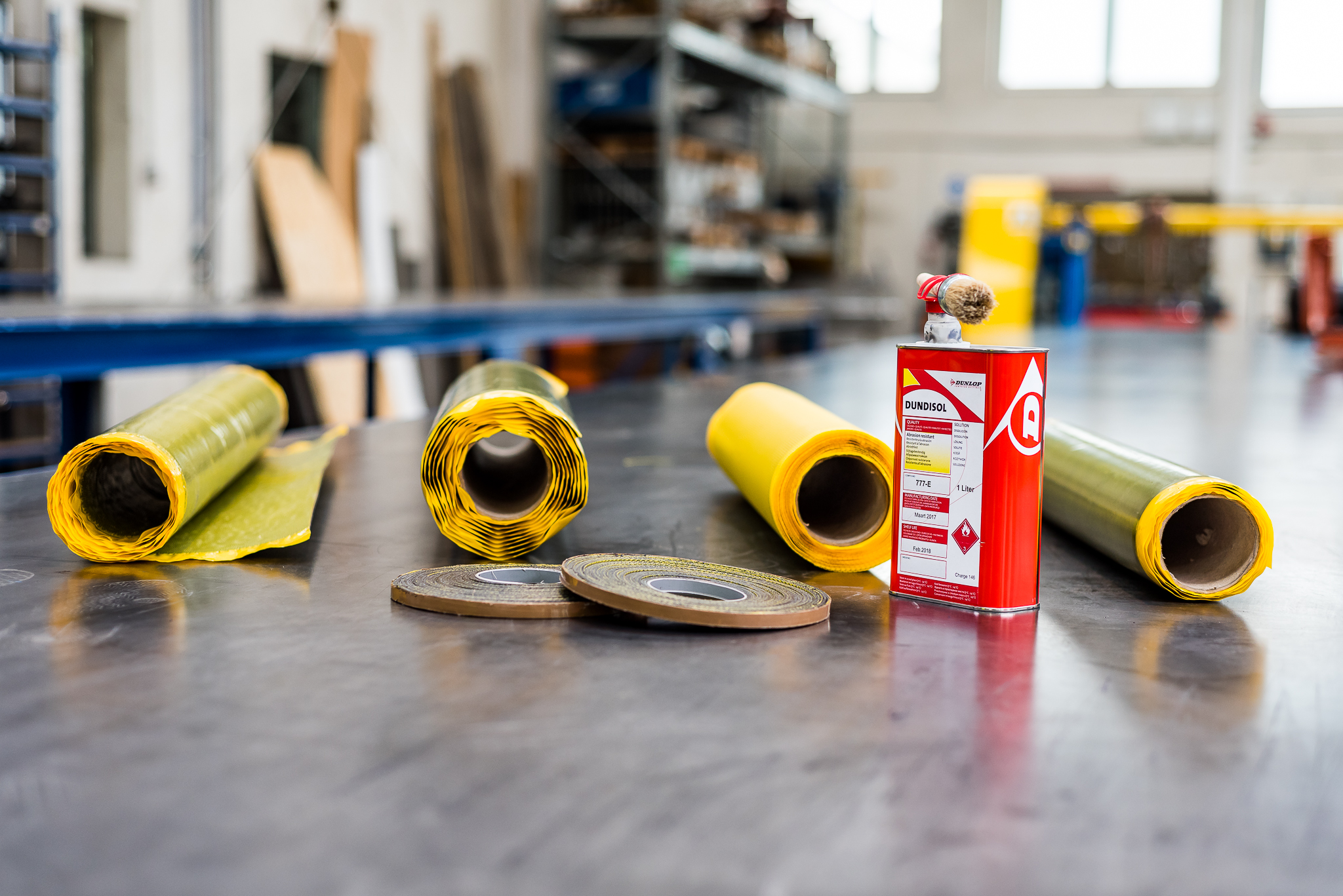
Splice Insights: The Materials
Fenner Dunlop proudly presents
Splice Insights: Material Compatibility
By: Buddy Wilson/Senior Director – Service Operations at Fenner Dunlop
Welcome back to #SpliceInsights: Fenner Dunlop’s five-part series focusing on vulcanized splicing. In this part, we are going to examine the importance of material compatibility and how it can affect the quality of the splice.
To begin, the global economy has led to an onslaught of conveyor belting products hitting the shores for consumption, and some may even say it has become a race to the bottom. The same is true for splice materials.
Despite the size or function of the belt, its reliability is critical to whomever is operating it. We must remember that reliability and overall production security is not only measured by the belt construction, compounding, etc., but with the reliability of its weakest link, the splice. It is here where we must decide if “good enough” is good enough?
Apples & Apples, or rather Red Apples & Green Apples
Let’s begin with the statement: All splice materials are not created equal.
That said, “apples and apples” comparison many times has turned into red apples vs. green apples. To clarify that train of thought is to understand that when dealing with splice materials, there is a range of specifications that are similar, but don’t necessarily match 100%.
Therefore, the only similarity is that “apple” is in the description. We know that may be convoluted, but if you follow the logic, it becomes clear. When the belt specification calls for specific splice materials to assure the splice performs up to expectations, are we willing to take a chance on materials that are only marginally compatible? This is the conundrum!
Some operators and purchasing personnel may not have the technical background or a general understanding that there could be a difference in what materials are used to splice their belt. They may assume that the materials provided by the service provider are 100% compatible to the belt being spliced.
While there are many top-quality producers in the third-party market, there are far more sub-standard producers trying to lure service organizations with low prices and no guarantee of compatibility with the belt. The only way to 100% guarantee material compatibility is to consult the belt manufacturer and procure those materials directly.
Wide Ranging Applications
Conveyor belting applications range from general purpose to unique applications with specific requirements. In any application, we are faced with the same realities as service providers. How do we best protect the weakest point (or points) along this conveyor belt?
Specialty applications, including MSHA, heat resistance, fire & oil resistance present completely different challenges when splicing. These belts must usually meet stringent regulatory and performance standards. This requires a more precise physical and chemical match between the splice materials and the parent belt. Given the application specific nature of such belts, it is prudent to utilize manufacturer produced splice materials that match the belt specification completely.
General Purpose Belt Constructions & Compounding (Fabric Carcass)
PIW Range: 220 PIW to 600 PIW
Compound Range: ARPM Grade 1
ARPM Grade 2
ARPM Oil Service* / MOR
Specialty Belt Constructions & Compounding (Fabric & Steel Cable)
PIW Range: 220 PIW to 6000 PIW
Compound Range: ARPM FR Class 1 (MSHA CFR30 Pt. 14)
ARPM HR Class 1 – 3*
Heat & Oil Service
Fire & Oil Service
*APRM classification based on specific ASTM testing standards
Duty to Our Customers
The effects of a global economy have impacted every industry – pushing the edict of cost savings as the primary driver for all products and services. In the same breath, our customers still demand excellence in performance from their conveyor belts.
Despite these factors, we as service providers must be prudent in selecting, not only the correct belt, but just as importantly, the correct splice materials. We, as manufacturers of engineered products and providers of world class service, must guard against the race to the bottom and deliver the best solution, and not something that is “good enough.”
In the next part of #SpliceInsights, we will be exploring the value and importance of splice tools and equipment. Follow us on social media to stay updated when new blog posts become available and click the subscribe button in the bottom right corner on your screen (if you use Google Chrome as your browser) .
Find your local distributor or Fenner Dunlop Conveyor Services location by checking out our interactive map here or reach out to us at info@fennerdunlop.com if you have any questions about vulcanized splicing!