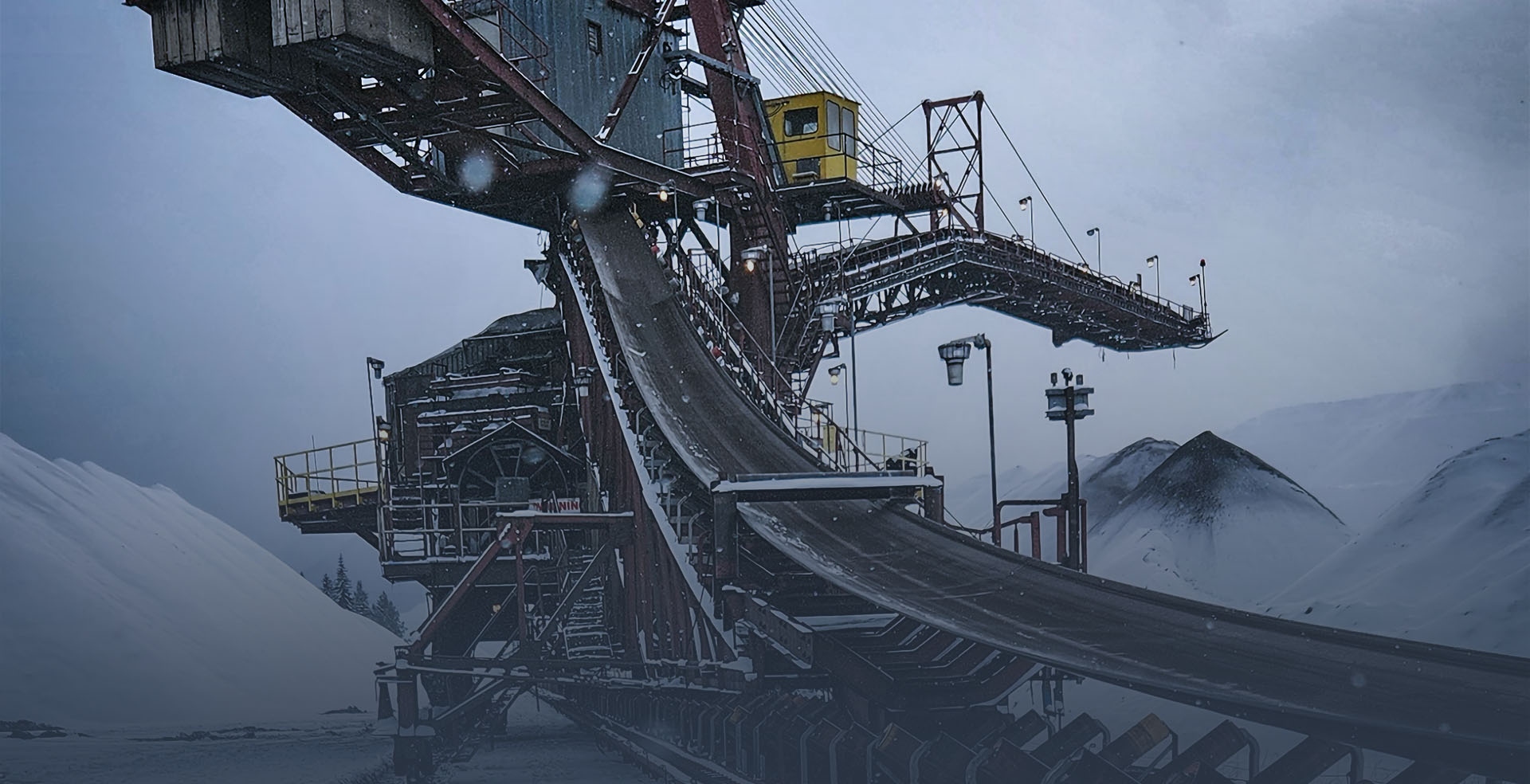
Turning Waste into Innovation: Teck, Tyromer, and Fenner Dunlop’s Journey to Sustainable Mining Solutions
Giant mining tires and conveyor belts are made from high-performance rubber, and historically, the perception that regenerated rubber cannot effectively replace virgin rubber has posed significant sustainability challenges in the tire and rubber industry.
Waste off-the-road mining tires (WOTR) represent a considerable sustainability issue due to high costs and logistical complexities. In some cases, only six tires can be shipped on a single transport truck. These highly engineered products are composed of natural and synthetic rubber compounds, numerous reinforced layers, and steel belts. A single haul truck tire can weigh up to 5 metric tonnes (11,000 pounds), stand 15 feet tall, and contain enough steel to manufacture a small car. However, like all tires, they eventually wear out. In Canada alone, thousands of these tires need replacement annually. With no national or international recycling programs or commercially viable recycling opportunities available, worn-out tires are among the largest sources of industrial waste generated by mining operations.
Research and Development of Mining Tire Recycling Technologies
While some companies repurpose retired OTR tires for temporary uses, such as building retaining walls or in civil engineering projects, about 80% either stockpile or dispose of these tires in landfills. This poses an enduring challenge, as OTR tires do not biodegrade due to their chemically inert materials. Whether left on-site or sent to landfills, OTR tires remain an environmental concern.
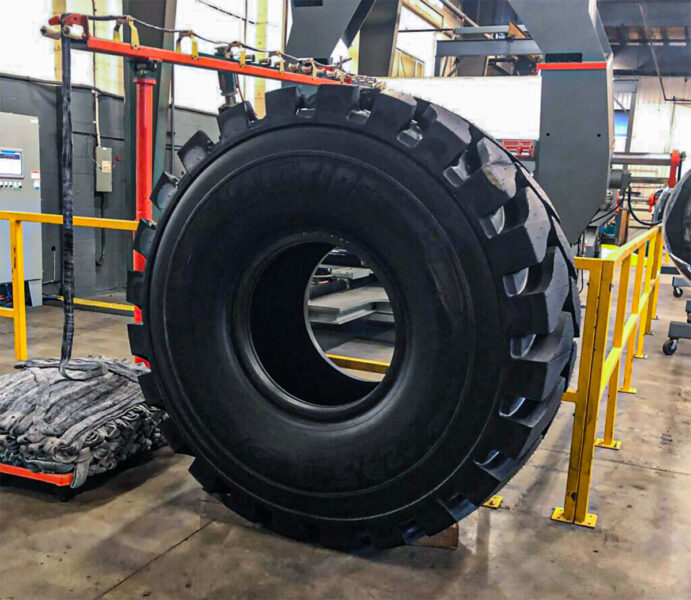
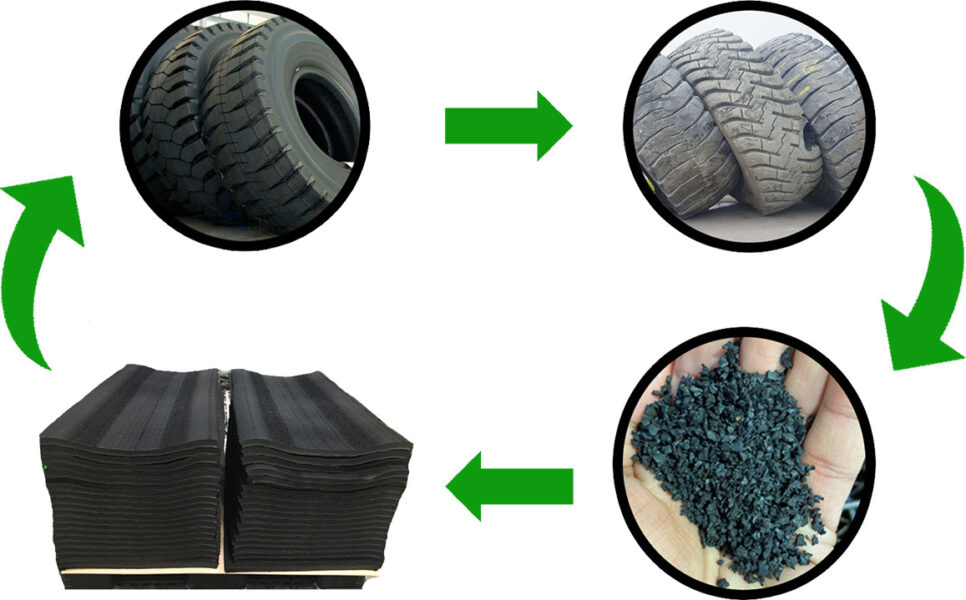
Environmental impact
To address this, the Teck team conducted extensive research on vendors capable of downsizing giant mining tires. They explored various technologies for reclaiming or regenerating rubber, including devulcanization, waterjet cutting, thermal conversion (pyrolysis), and micronization, among others. These technologies were evaluated based on their environmental impact—zero waste, energy usage, and greenhouse gas emissions. Ultimately, devulcanization and waterjet technologies emerged as the most promising options.
transform waste into quality rubber
The team prioritized finding an environmentally friendly and sustainable method for transporting the tires. They implemented backhauls (utilizing trucks returning empty) and used rail transport for materials. They also aimed to upcycle the rubber crumb beyond landscape mulch and rubber mats, intending to displace imported virgin rubber. This reclaimed rubber crumb was processed using devulcanization technology.
The goal was to develop technology that could transform waste into quality rubber that end users would adopt. Using Tyromer technology, they successfully created tire-derived polymer (TDP).
Teck collaborated with strategic partners, including Liberty Tire, to mechanically separate OTR tires, recycle the steel components, and provide the residual crumb rubber. This crumb was then upcycled using Tyromer’s devulcanization technology.
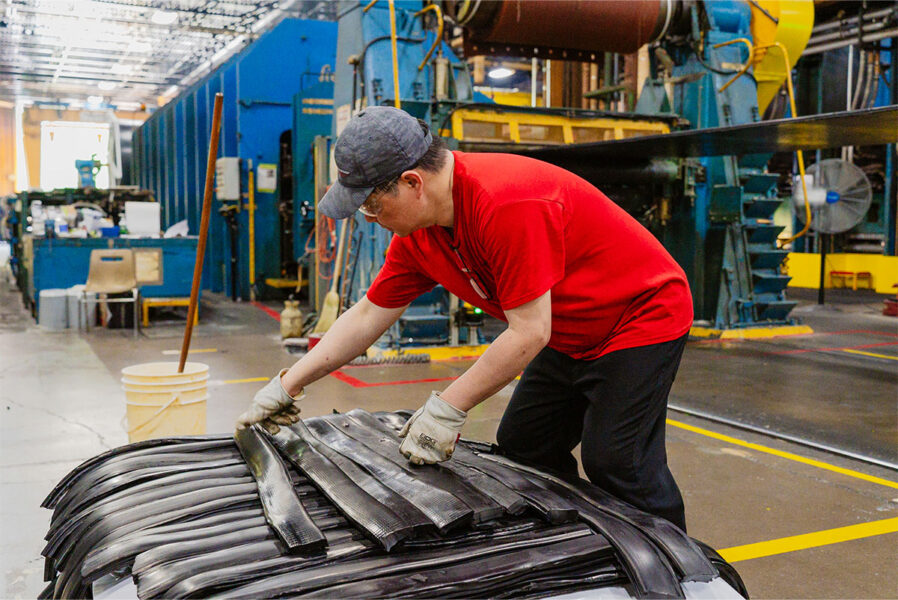
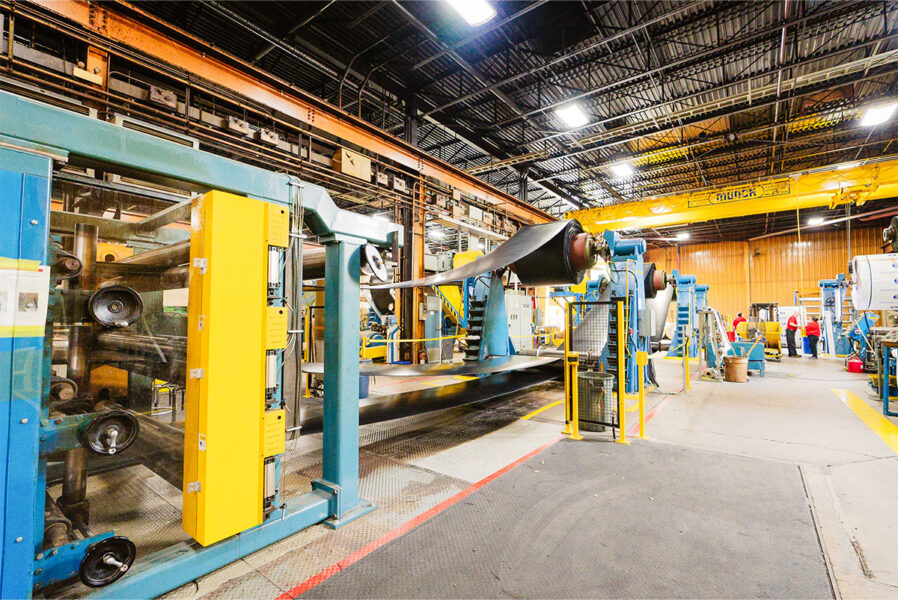
REGENERATED Rubber in New Products
Fenner Dunlop incorporated the TDP into new conveyor belts, which underwent compounding and rigorous testing phases. These belts were deployed and monitored at one of Teck’s mining operations in British Columbia. Gaining acceptance from management and maintenance teams required persistence and technical assurances from the manufacturer, as the stakes were high; any premature failures could result in costly downtimes at Canada’s largest open-pit copper mine, potentially jeopardizing future initiatives.
Following the initial pilot, the project expanded, with belts tested at multiple Teck sites and monitored for abrasion resistance and performance. The success of these early efforts led to the development of a new fire-retardant compound, requiring CSA certification from a third party. The culmination of this work was a 3,368-foot conveyor belt weighing 63,318 pounds, installed at one of Teck’s mining operations.
Teck’s careful and innovative approach enabled collaboration with industry leaders like Michelin and Fenner Dunlop, shifting perceptions in the conservative tire and rubber sector. Demonstrating that regenerated rubber can substantially replace virgin rubber marks a significant advancement, reducing the environmental footprint of mining operations and promoting circular economy principles in industrial manufacturing.
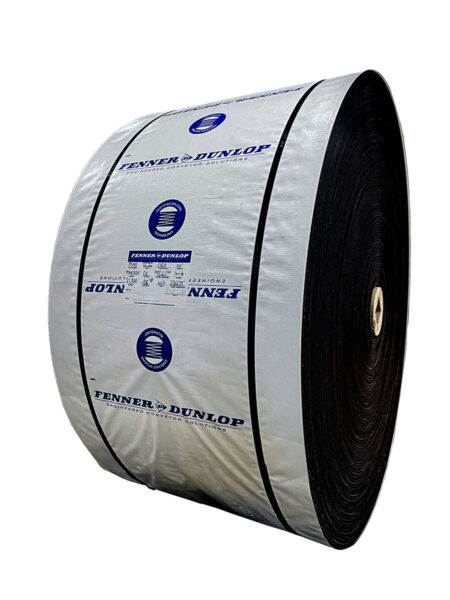
The Future of Circular Economy
In addition to meeting sustainability goals and contributing to the circular economy, Teck’s innovative pilot projects have set new industry standards, proving the concept of transforming waste into valuable resources. These efforts help prevent deforestation associated with rubber cultivation by providing a sustainable domestic alternative to imported rubber, significantly reducing Canada’s manufacturing sector’s reliance on foreign materials.
In conclusion, Teck’s pioneering efforts, in collaboration with industry leaders like Fenner Dunlop, not only highlight the potential of regenerating rubber to transform waste into valuable resources but also set a precedent for sustainable practices within the mining and manufacturing sectors. By demonstrating that high-performance products can be created from recycled materials, this initiative challenges conventional perceptions and paves the way for a more circular economy.