Manufacturing for a Sustainable Future
Sustainable Process:
- Recognize the importance of sustainable raw materials and optimizing production processes
- Proprietary highly efficient and sustainable manufacturing processes in four state-of-the-art manufacturing facilities
Resource Optimization:
- Optimize consumption of natural resources in our production
- The most upcycled, earth-friendly materials and compounds used in the industry
Product Quality:
- Continue to develop high-performance conveyor belts requiring fewer plies utilizing less materials without compromising durability
- Lighter and more energy efficient products that last longer and are more sustainable
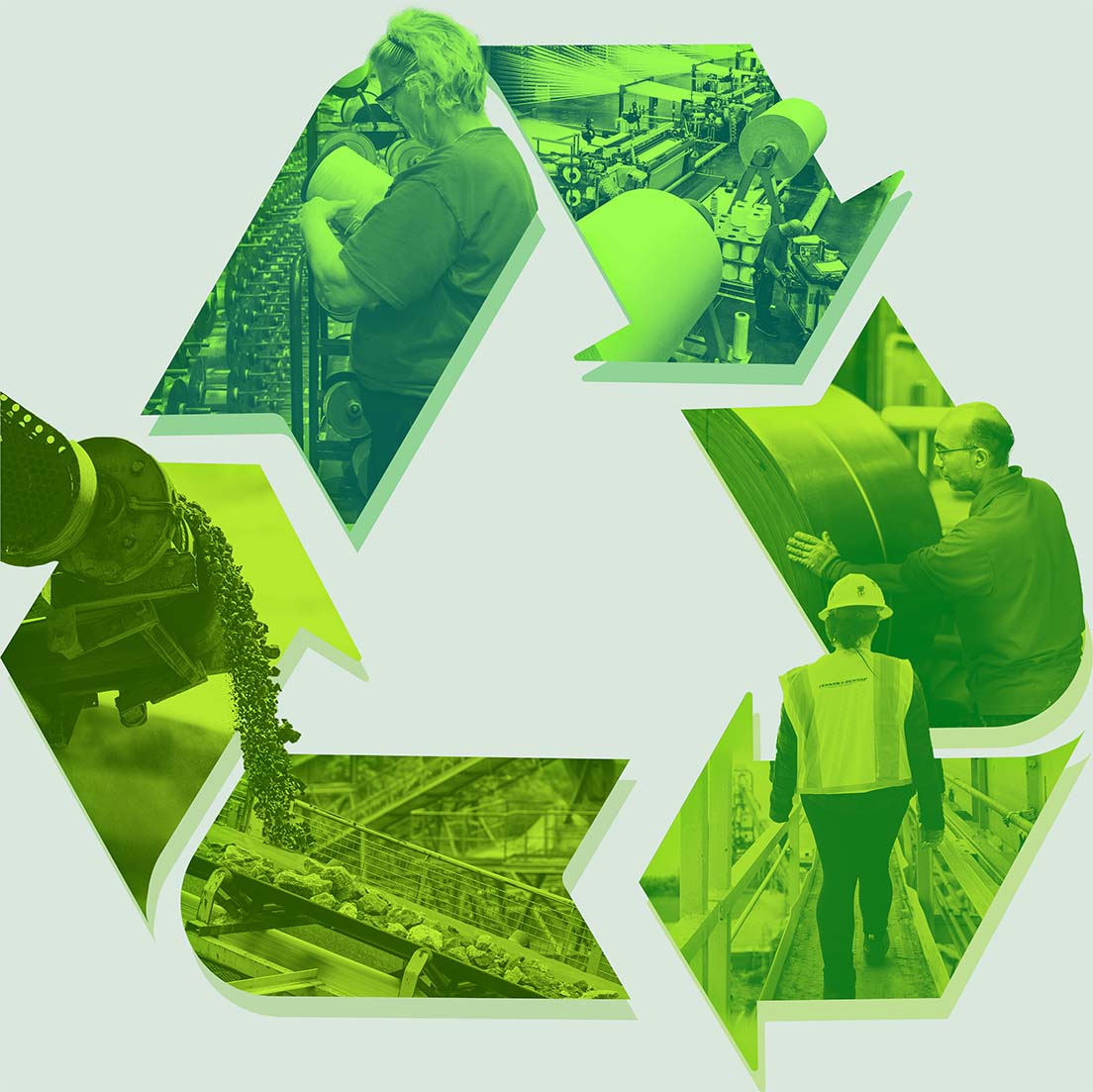
Environmental Targets
Ambition | Metric | Goal |
---|---|---|
Reduce our CO2 emissions | CO2 emissions | 50% by 2030 |
Improve the energy efficiency of our products | Energy efficiency of our products |
10% by 2030 |
Set the global standard for the environmental footprint of manufacturing facilities | Environmental footprint of facilities |
1/3 reduction by 2030 |
Ensure that the materials used in our products are renewable or recyclable | Renewable or recyclable materials used |
40% by 2030 100% by 2050 |
Use only deforestation-free natural rubber volumes | Deforestation-free natural rubber |
100% by 2030 |
We recognize the importance of focusing our sustainability commitment into every aspect of our company
The Life Cycle
of a Conveyor Belt
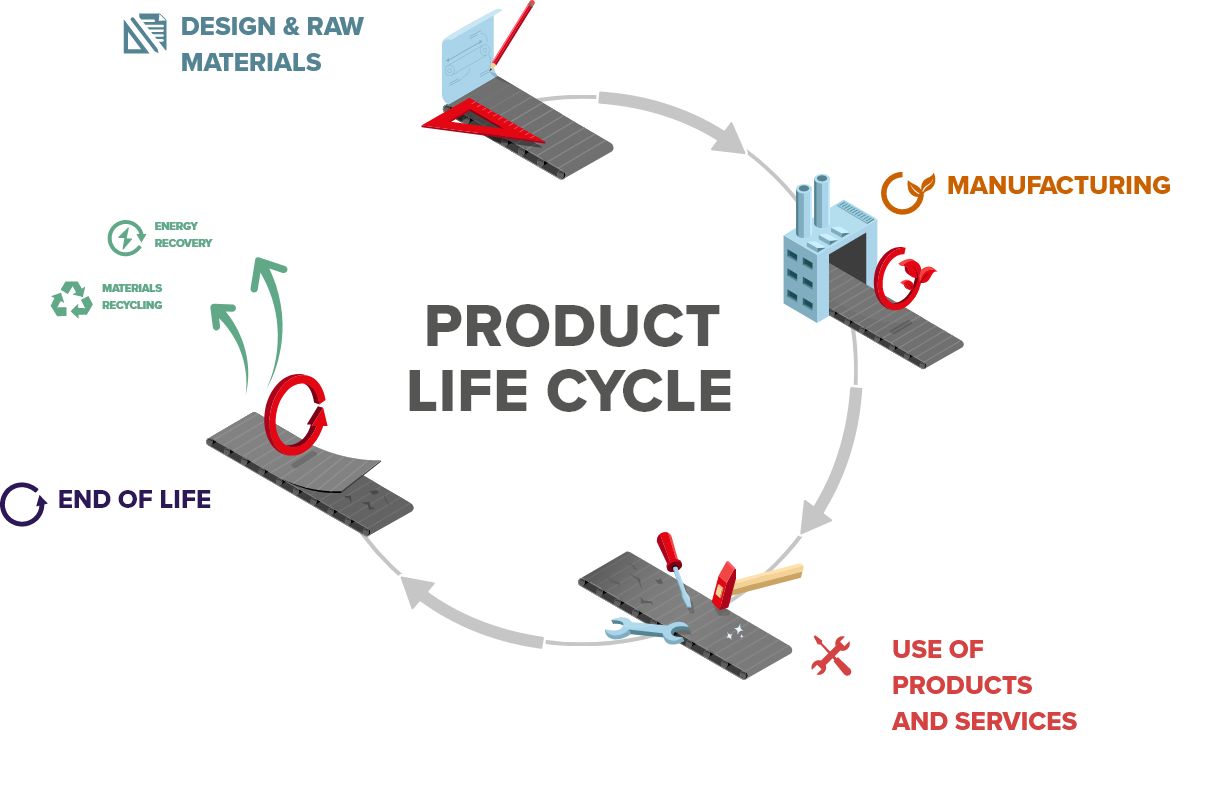
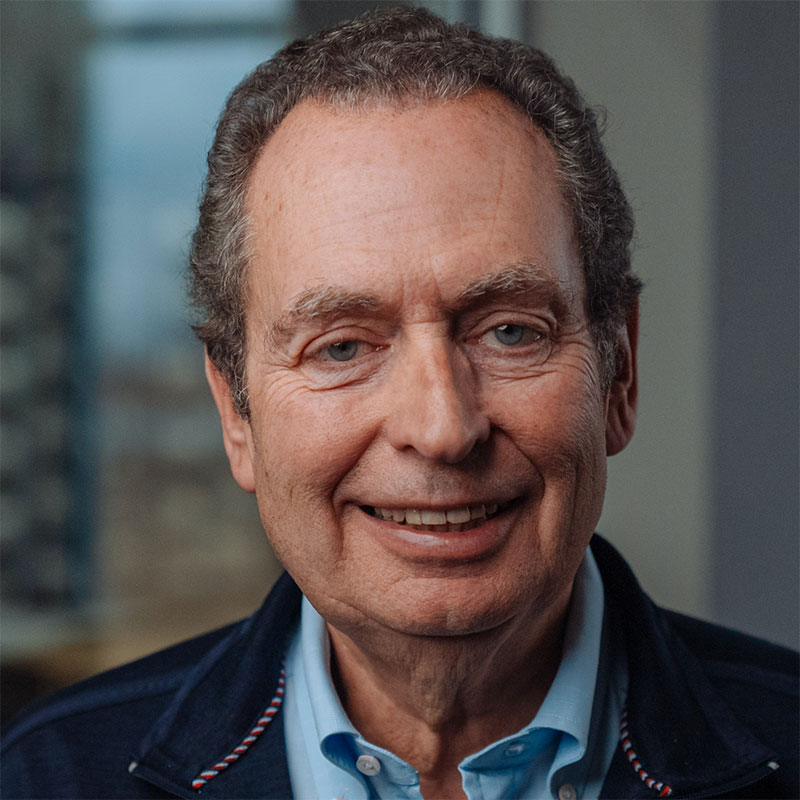
Proud Fenner Dunlop Employee Since 1976
We're looking to maintain sources of raw material for the future where ever possible using bio-based materials and also using recycled materials in the product without detriment to durability.
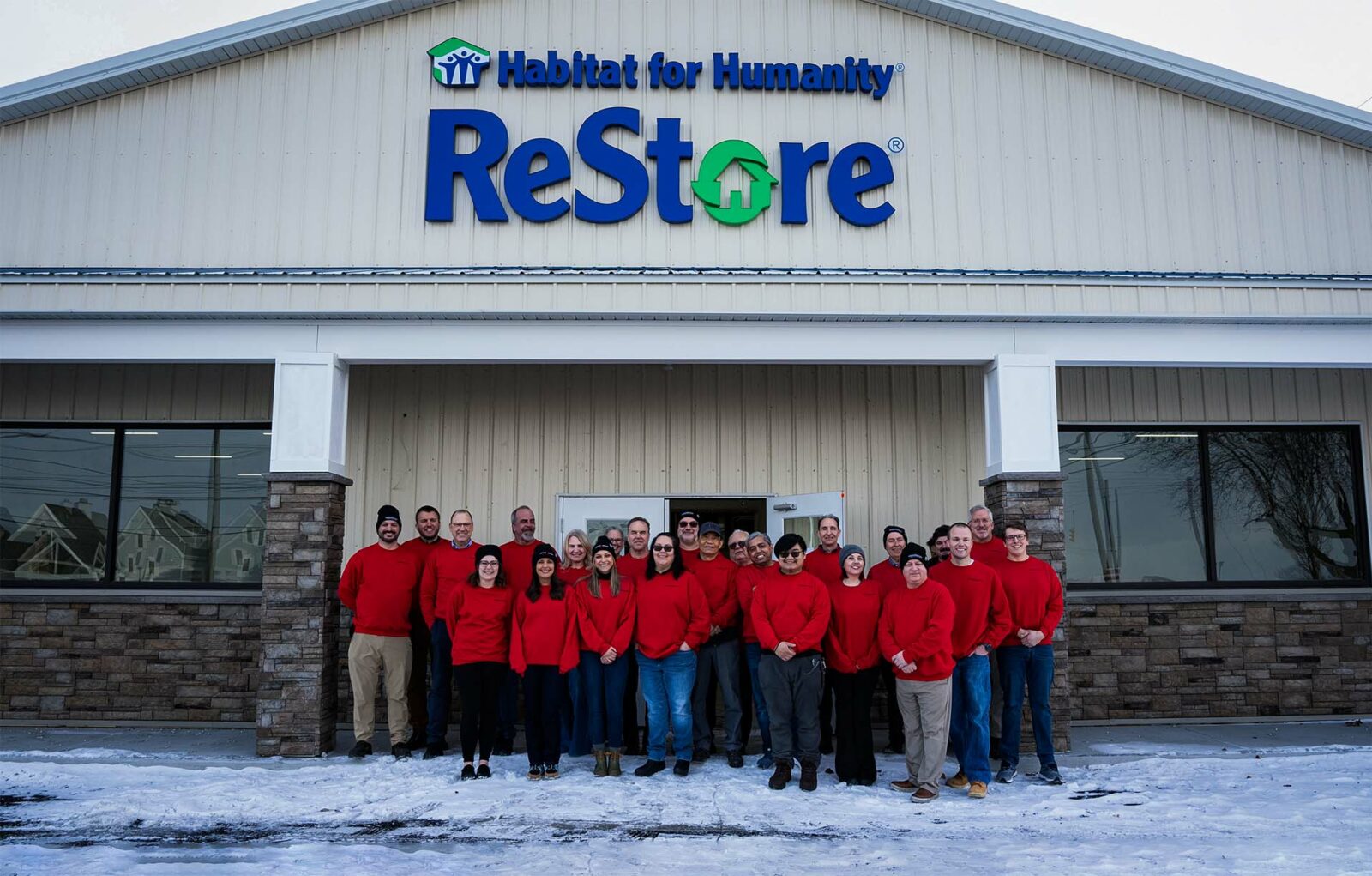
Giving Back to
Our Communities
At Fenner Dunlop, we believe in making a meaningful impact in the communities where we live and work. As part of our commitment to social responsibility, we offer all employees a paid day each year to volunteer and give back. Our team has proudly contributed to a variety of initiatives, including:
Supporting mine reclamation efforts by planting trees and removing invasive weeds
Building and donating bicycles to individuals without reliable transportation.
Stocking local food banks with essential groceries and packaging meal kits for families in need.
Volunteering at Habitat for Humanity, becoming the first large group to support the new Port Clinton, OH site.
These projects reflect our values and the pride we take in being more than a manufacturer—we’re active neighbors, partners, and contributors to the communities we serve.
Diversity Targets
-
A company that allows diversity to flourish in all its forms (*IMDI)
by 2023
72/100
by 2030
80/100
*IMDI, a composite indicator tracking inclusion and diversity)
-
Percentage of women in management and supervisory positions
by 2023
30.1%
by 2030
35%
Other Business Targets
-
Employee and contractor health and safety /Engagement rate*
by 2023
84%
by 2030
85%
*IMDI, a composite indicator tracking inclusion and diversity)
-
A company where everyone feels physically safe at work / TCIR**
by 2023
1.01
by 2030
<0.5
**Total Case Incident Rate
United Nations 17 Standards in
Sustainability Development
sustainable development goals
The 2030 Agenda for Sustainable Development, adopted by all United Nations Member States in 2015, provides a shared blueprint for peace and prosperity for people and the planet. At its heart are the 17 Sustainable Development Goals (SDGs), an urgent call for action by all countries. Our Group uses these standards to gauge our success in climate impacts, resource use, and biodiversity. We engage our employees and customers to use resources efficiently while preserving them for future generations. These goals aim to end poverty, improve health and education, reduce inequality, spur economic growth, tackle climate change, and preserve oceans and forests.