X Series is 3x more impact resistant and 5x more rip resistant so the belt can last longer vs. traditional plied belting
Product Ideation:
The X Series was developed to solve the everyday challenges encountered by conveyor operators using traditional plied belting, specifically aiming to alleviate pain points such as premature damage.
Redefining Belt Strength:
Through intricate weaving and treating, our X Series conveyor belts are precisely engineered to withstand rip, tear, and impact damage, surpassing the longevity of traditional plied belts. By leveraging the inherent strength of the fabric, we eliminate the need for additional rubber skim layers in the belt’s construction.
Transforming Operations:
The X Series gives our end users the power to better manage their operations with maximum uptime, reduced need for replacement belts, enhanced productivity, and a lower total cost of ownership.
Compare the X Series product line to determine the best solution for your application
This chart is a guideline for selecting Fenner Dunlop’s X Series but should not be used as the sole tool for belt selection. We strongly recommend collaborating with Fenner Dunlop's sales and technical team for best belt selection.
Heavy-Duty Applications
Single Unit UsFlex: 440 PIW and up
Dual Unit UsFlex: 660 PIW and up
Medium-Duty Applications
Single Unit Nova-X: 440 PIW-600 PIW
Lighter-Duty Applications
Single Unit Ultra X: 275 PIW-350 PIW
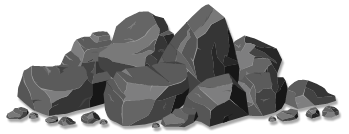
Handles materials 12"+
depending on drop height
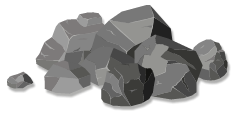
Handles materials 3"– 8"
depending on drop height
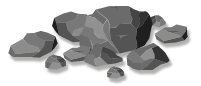
Handles materials 3" and below
depending on drop height
8 ft.+
Withstands impact punishment from drop heights up to 8’+
2 – 6 ft.
Withstands impact punishment from drop heights between 2’ to 6’
< 2 ft.
Withstands impact punishment from drop heights below 2’
Recommended for conveyors during the first steps of the operation such as for high abuse and high impact applications including conveyors under primary crushers.
Recommended for conveyors during the middle steps of the operation including applications such as secondary/tertiary, transfer points, overland and general flow throughout the operation.
Recommended for conveyors during the final steps of the operation such as movement of smaller and less sharp material with shorter drops.
Straight-Warp
Carcass
Dual-Crimp
Carcass
Dual-Crimp
Carcass
This could be your operation too!
Hear from highly satisfied X Series enthusiasts.